Sustainable Innovative Packaging
Anchor Packaging offers our customers environmentally neutral products produced in a sustainable manufacturing environment. Anchor recycles virtually 100% of its raw materials and continues to minimize our product designs to reduce waste and shipping fuel costs.
Original Source: Environmental Protection Agency Solid Waste Management Hierarchy

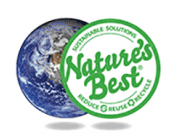
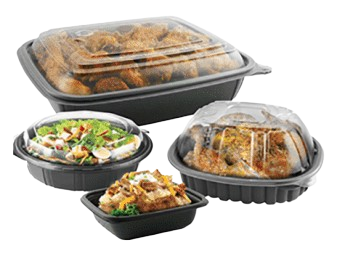
- Reduce: Our product development team has greatly reduced the use of petroleum based resins in our products through design, process and material engineering without sacrificing performance. Some of our products have seen reductions in resin of up to 40%! Other rigid products use a minimum of 10% post-consumer RPET. PVC cling film includes 12% epoxidized soy bean oil (ESBO); meat film 5-8% ESBO. Cores are made with 100% recycled paperboard.
- Reuse: Anchor Packaging was the first to introduce the “green” concept of REUSE, then recycle polypropylene takeout packaging. The EPA recommends REUSE over many other waste management strategies.
- Recycle: Anchor’s rigid plastic products are made of A PETE/RPET and polypropylene. PETE is the most recycled food packaging material nationwide. Polypropylene is also eligible for recycling in many communities along with aluminum foil. Dri-GardTM on film Cutterboxes is non-toxic water based polymer coating certified by Fibre Box Assoc. for recyclability. Check your community for recycling information (www.earth911.org).
- Recover (stored energy): Anchor polypropylene products, when safely incinerated in a waste-to-energy facility, produce the highest per ton BTU energy value of any waste material: 38 million BTUs per ton. This is twice the energy value of coal, the primary source of electric power generation in the U.S.
Environmental Impact – Operations
Significant reductions in energy usage continue to reduce the carbon footprint of our manufacturing and distribution facilities. More than a 63% reduction in electricity continues following the replacement of fluorescent with LED lights at all locations and the rebuilding of capacitation banks to improve the power factor from the mid-80s to 93% or above. Oil-free compressors with energy-efficient technology replaced older equipment, thus reducing the consumption of fossil fuel products and also reducing energy consumption, which further reduces carbon footprint. Installation of sonic air listening devices enables the facility to locate and repair air leaks, also reducing energy consumption. These changes reduced our electrical profile and our costs from a “Large” to “General Time of Use” customer of Entergy. Our environmental footprint was further reduced by the elimination of 150 truckloads of purchased cores for our cling film. These film cores are now made internally by our plant with 100% recycled paperboard.

Nature’s Best
Watch for the “Nature’s Best” trademark on products that include post-consumer recycled RPET for cold foods and for packages with natural mineral additives reducing the use of PP resin by 40% for use with hot or cold foods.
Reuse
The EPA advises that REUSE and REDUCE on the pyramid are the most preferred methods of waste management.